LOW PLASTICITY BURNISHING (LPB®)
WORLD-CLASS LABORATORY
SHOT PEENING OPTIMIZATION
AWARDS AND CERTIFICATIONS
TECHNICAL PAPERS
CONTACT
Lambda Technologies Group includes Lambda Research, a world-class materials testing laboratory, and Surface Enhancement Technologies, inventors of Low Plasticity Burnishing (LPB®). Lambda specializes in the understanding, measurement and control of local residual stresses to provide complete surface enhancement solutions.
LPB is an effective, validated design and repair solution widely applied to jet engines. It is now available and proven for compressor components in stationary turbines threatened with fatigue failure from stress corrosion cracking, foreign particle damage, erosion, corrosion, or fretting damage.
Validated Repair Solution
LPB has been specifically proven in the field as an effective repair technique for plant applications including, but not limited to:
- Erosion damage on R0 compressor blades of the 7FA and 9FA gas turbines
- Foreign particle object damage (FOD) of 7th stage compressor blades in 501F gas turbines
- Stress concentration damage of 1st stage compressor blades in Taurus 70 gas turbines
- Moisture-induced erosion and high cycle fatigue damage of low-pressure steam turbine blades
- Fretting damage on rotor through bolts in 501G-class gas turbines.
Low Plasticity Burnishing
LPB® is a mechanical process that imparts a designed residual stress field into the surface of components to produce a deep, stable layer of beneficial residual compression.
The depth, magnitude, and distribution of the compression are designed specifically for each component and application, producing minimal cold work.
LPB can sculpt designed levels of compression onto a component surface ranging from a few thousandths of an inch (comparable to shot peening) to approximately half an inch.
LPB is an in-shop surface treatment option available for a variety of rotating and stationary turbine components, including blades, vanes, disks, rotors, rotor bolts, and others.
Benefits of LPB
- LPB is easily performed with conventional CNC machine tools or robots
- LPB can be implemented during initial manufacturing or during maintenance/repair operations
- Applying LPB can avoid the wholesale component replacements often recommended by OEMs
- LPB is easier to implement, less complicated, and more precisely controlled than laser shock peening (LSP)
- LPB increases the time in service for components, decreasing maintenance & replacement costs
Learn more about LPB’s awards and certifications or read our technical papers on LPB technology.
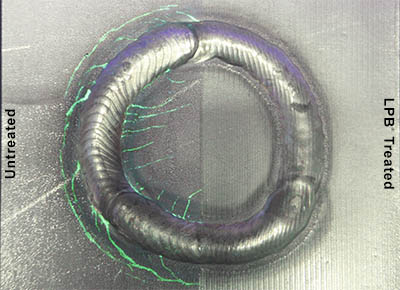
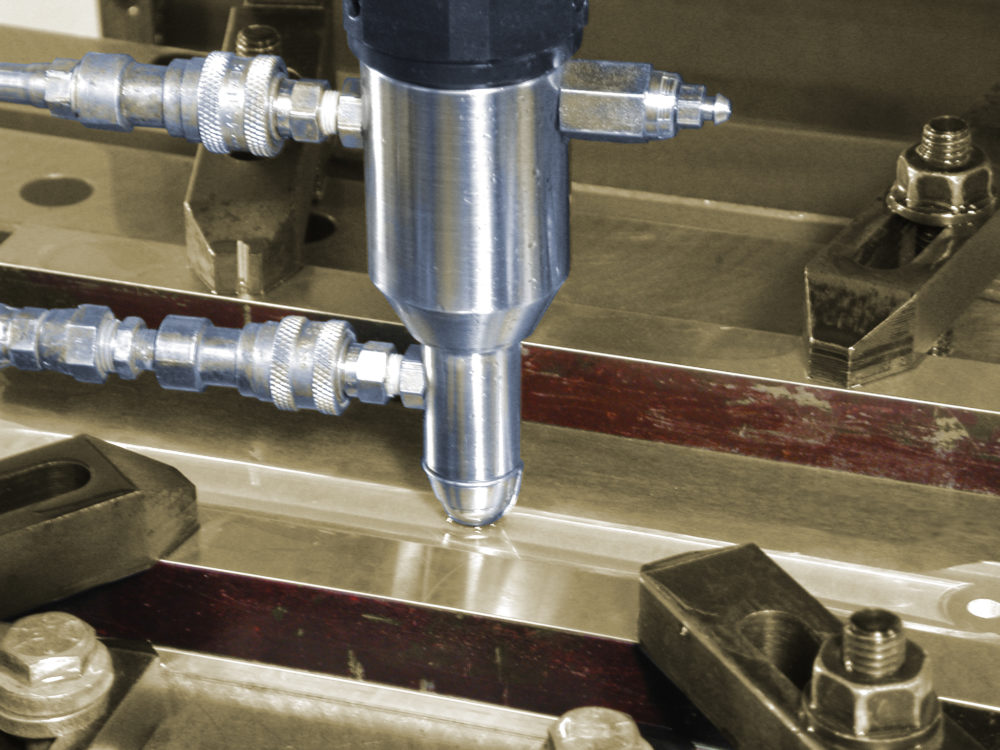
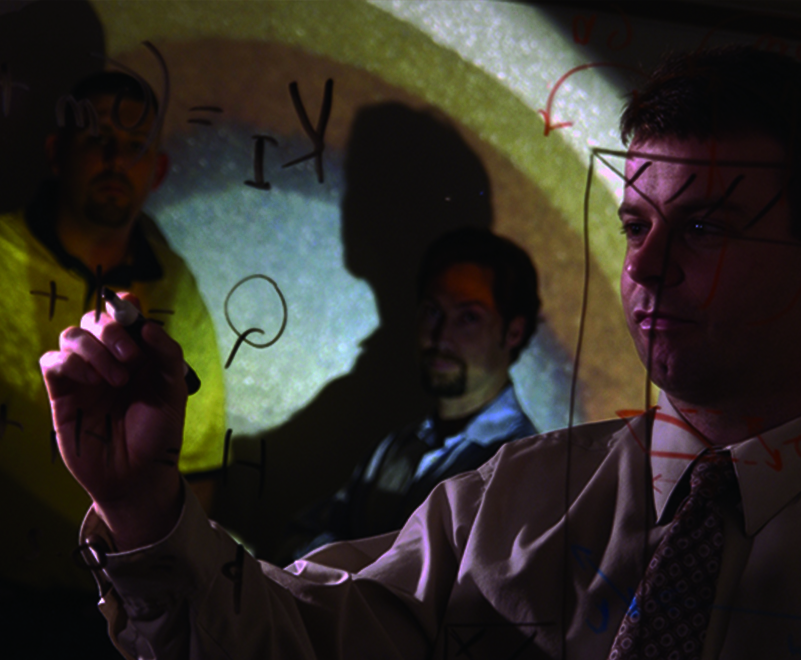
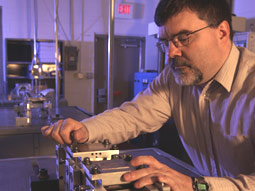
World-Class Laboratory
Lambda Research, Inc., part of Lambda Technologies Group, is a world-class ISO 17025 accredited materials testing facility, specializing in residual stress measurement and analysis.
With over 200 years of combined experience and nearly a million completed measurements, Lambda is a name people trust.
Residual Stress Measurement – Preeminent source of residual stress measurement
Fatigue Testing – High cycle and low cycle fatigue testing, as well as rolling contact fatigue tests to characterize the influence of residual stress and cold work on fatigue strength
Corrosion Testing – General corrosion testing, alternate immersion tests per ASTM 644, stress corrosion cracking (SCC) testing, polarization testing, and metallographic analyses
Failure Analysis – State-of-the-art equipment and advanced modeling techniques to establish failure mechanism, calculate the stresses at failure and provide a complete history of crack growth in your component.
Retained Austenite Measurement – Lambda is the only accredited, independent laboratory using Bragg-Brentano diffractometers in strict adherence to ASTM E975 and SAE SP-453 specifications.
Shot Peening Optimization
Lambda Technologies Group also offers shot peening optimization services for turbine operators.
This specialized service from Lambda allows the peening specifications of any component to be tailored to achieve optimum fatigue results with the fastest processing times.
Both empirical and analytical studies confirm that a full, 100% shot peening coverage may not be necessary and may not provide the best fatigue performance.
By developing specifications that reduce repeated media impacts, critical components may benefit from lower surface cold work.
Benefits of Shot Peening Optimization
- Up to 5X improvement in production times
- Improved fatigue performance
- Reduced capital investment
- Reduced peening equipment wear and tear
- Reduced media consumption
- Improved thermal stability
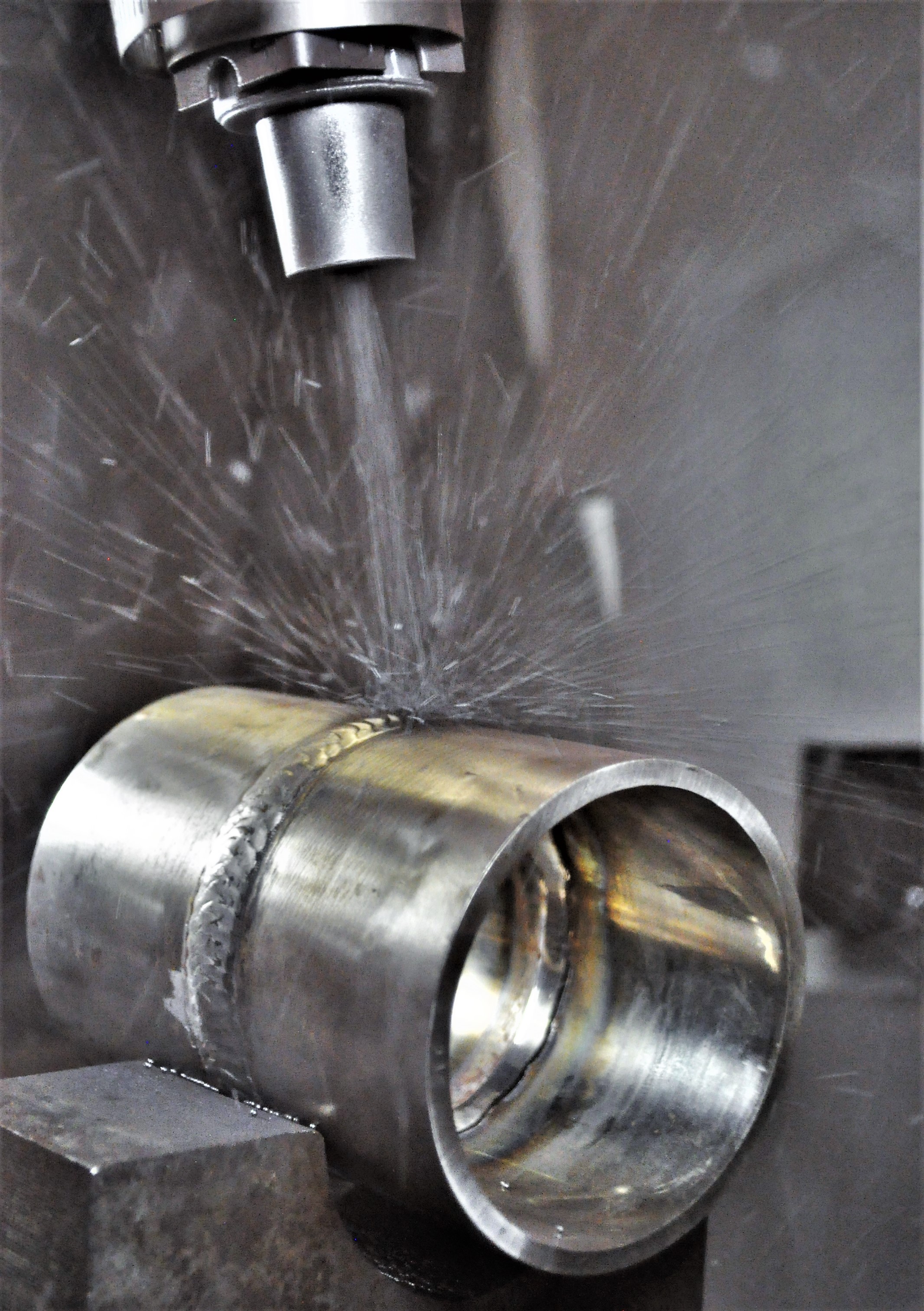
Awards and Certifications
LPB® is an award-winning technology that has received the R&D 100 Award for revolutionary ideas in science and technology, the John P. Davis Award from the International Gas Turbine Institute (IGTI), and the NASA Hallmark of Success Award.
The Electric Power Research Institute (ERPI) issued a report on Improving Compressor Airfoil Damage Tolerance: Evaluation of Compressive Layer Surface Treatment. In it, they stated:
“Low plasticity burnishing was used to apply an equivalent compressive patch to the leading edge of retired blades. The burnished blade’s residual stress measurements met or exceeded the compressive layer depth and magnitude of the originally applied laser shock peened compressive patch.”
AS9100
ISO 9001:2015 Certified
FAA Accepted Process
Accepted Process of the U.S. Air Force Engine Structuring Integrity Program (ENSIP)
Approved Supplier for NAVAIR, Pratt & Whitney, Delta TechOps, and GE Aviation
Learn more by reading our technical papers.
Technical Papers
Lambda is a well-known resource for research and education on residual stress.
Read our technical papers on LPB technology, including two that won the International Gas Turbine Institute’s John P. Davis Awards in 2007 and 2003.
- *Award Winner* Mitigation of Fretting Fatigue in Blade and Disk Pressure Faces with Low Plasticity Burnishing (LPB)
- *Award Winner* Case Studies of Fatigue Life Improvement Using LPB in Gas Turbine Applications
- Fatigue Life Extension of Steam Turbine Alloys Using Low Plasticity Burnishing (LPB)
- Improving Corrosion Fatigue Performance & Damage Tolerance of 410 Stainless Steel via Low Plasticity Burnishing (LPB)
- FOD Resistance and Fatigue Crack Arrest in Low Plasticity Burnished (LPB) IN718
Contact Us
Effective and affordable repair techniques are essential to maintaining financial and mechanical health in the power industry.
Contact us to learn more about the LPB® process for repairing compressor components in stationary turbines or any of Lambda’s world-class laboratory services.