Certifications & Accreditations
Surface Enhancement Engineering (Surface Enhancement Technologies LLC)
AS9100
AS9100 Rev D Quality Management Systems Certification for the design, engineering, and implementation of surface enhancement technologies including patented and proprietary Low Plasticity Burnishing (LPB®) for military, aviation and aerospace. (See Certificate)
ISO 9001:2015 Certified
The Quality Management System applicable to the engineering and implementation of surface enhancement technologies including patented and proprietary Low Plasticity Burnishing (LPB®) has been assessed and registered as conforming to the requirements of ISO 9001:2015. (See Certificate)
FAA
Surface Enhancement Technologies is a certified FAA 145 Repair Station. (See FAA 145 Certificate)
Low Plasticity Burnishing is FAA Accepted for repair and alteration of aircraft components. (See FAA Acceptance Letter)
ENSIP
Low plasticity burnishing (LPB®) is an accepted process of the US Air Force Engine Structural Integrity Program (ENSIP), MIL-HDBK-1783B.
Approved Supplier
Lambda Technologies is an approved supplier for NAVAIR, Pratt & Whitney, Delta TechOps, and GE Aviation.
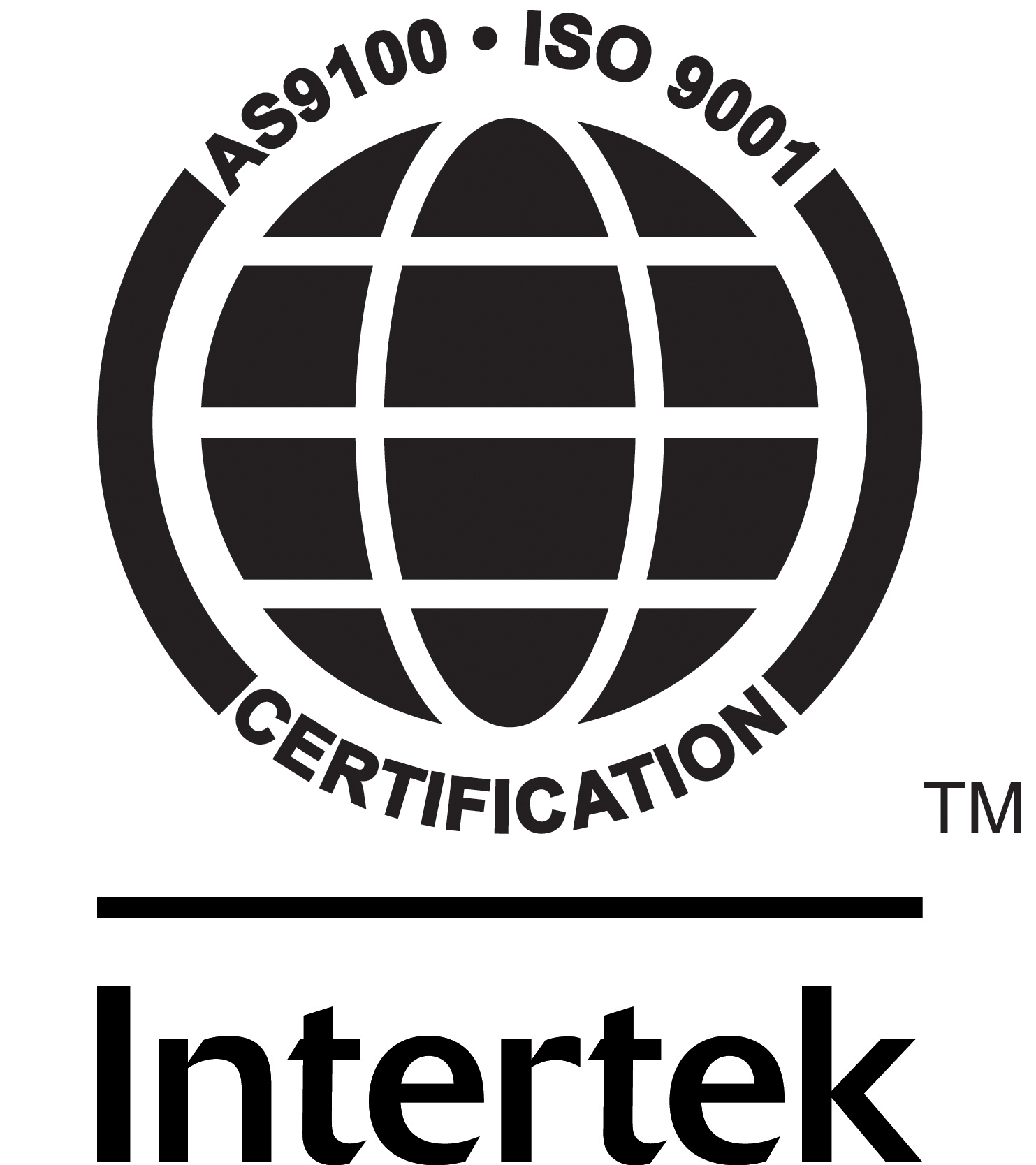
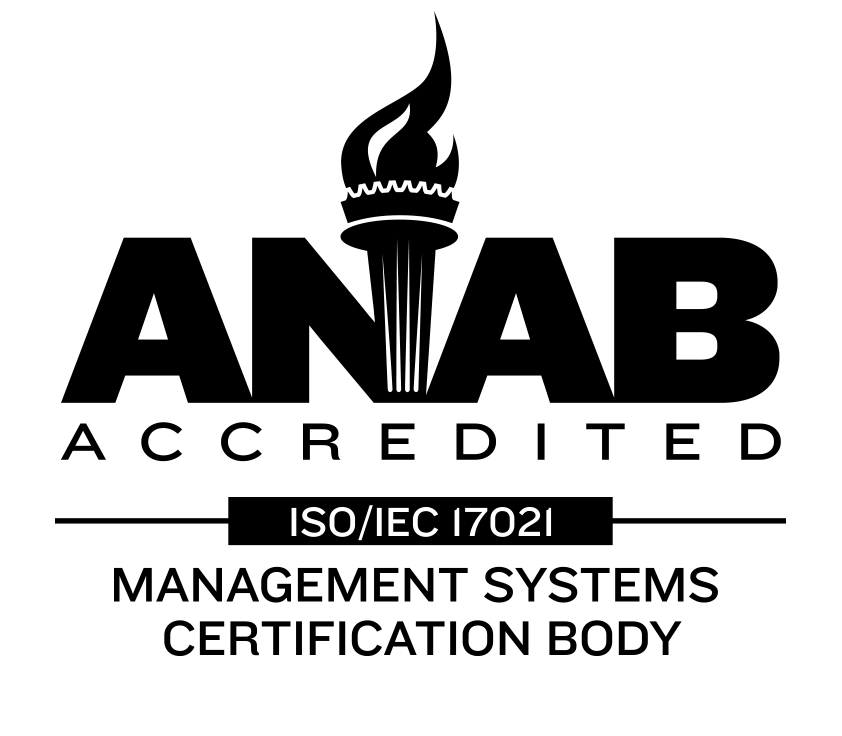
Laboratory & Engineering Services (Lambda Research Inc.)
Current A2LA Certificate in PDF format
Lambda Research has been certified by many major corporations for meeting their specific criteria for materials testing, including General Electric (S400), Honeywell, Rolls Royce, and Babcock & Wilcox. Lambda is the only S400 lab in the world certified by General Electric to perform residual stress measurement.
Lambda Research is an approved supplier of design verification for Rolls Royce.
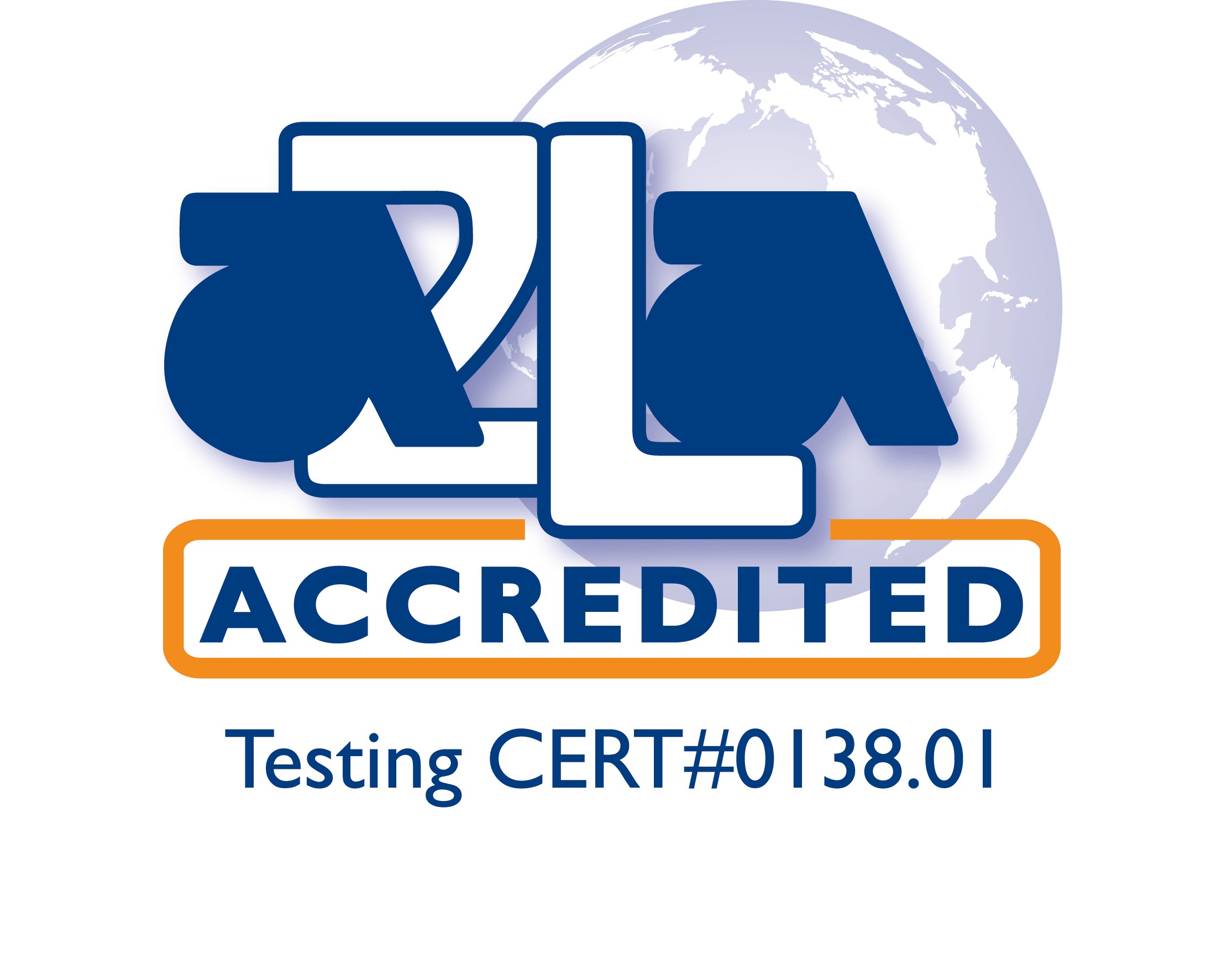
Testing Certifications
Lambda is capable of performing measurements to the following standards:
SAE HS 784
– Residual Stress Measurement by X-Ray Diffraction
Manual containing detailed and comprehensive theoretical background of x-ray residual stress measurement techniques as well as best means of applying these techniques in the practice for accurate and useful results.
SAE SP-453
– Retained Austenite and Its Measurement by X-Ray Diffraction
Paper providing detailed information for control and proper measurement of retained austenite via x-ray diffraction.
GE 4013195-991
– Residual Stress Measurement by X-Ray Diffraction
Standard method for controlling the measurement of residual stress for General Electric parts and specimens. Specific measurement requirements and parameters are given.
ASTM F2024
– Standard Practice for X-ray Diffraction Determination of Phase Content of Plasma-Sprayed Hydroxyapatite Coatings
Practice for the determination, by the Reference Intensity Ratio External Standard Method, of the percent by weight of the crystalline phases, hydroxyapatite (HA), beta-(whitlockite) tricalcium phosphate (β-TCP), and calcium oxide (CaO) in coatings deposited upon metallic substrates by plasma spraying hydroxyapatite.
GE S-400
– Certified Materials Test Laboratories (CMTL): Metallic Materials
Quality specification establishing disciplines required by General Electric (GE) Aviation for Certified Materials Testing Laboratories (CMTL). This includes both Independent and Embedded/Captive Testing Laboratories. GE Aviation oversight and approval of a lab is dependent on more than one element. These elements may include on-site audit by GE or a third party and round robins or other proficiency demonstration processes.
ASTM E81
– Standard Test Method for Preparing Quantitative Pole Figures
Test method covering the use of the X-ray diffractometer to prepare quantitative pole figures.
GE 40132040-860
– Residual Stress Measurement by X-Ray Diffraction
Provides a standard method of residual stress measurement for General Electric (GE) metallic parts and specimens.
ASTM E837
– Standard Test Method for Determining Residual Stresses by the Hole-Drilling Strain-Gage Method
Test method specifying a hole-drilling procedure for determining in-plane residual stresses near the surface of an isotropic linearly elastic material.
ASTM E915
– Standard Practice for Verifying the Alignment of X-Ray Diffraction Instruments for Residual Stress Measurement
Practice describing the procedure for verifying the alignment of X-ray diffraction instruments used for residual stress measurements.
ASTM E1237
– Standard Guide for Installing Bonded Resistance Strain Gages
Standard providing guidelines for installing bonded resistance strain gages.
ASTM E975
– Standard Practice for X-Ray Determination of Retained Austenite in Steel with Near Random Crystallographic Orientation
Practice covering the determination of retained austenite phase in steel using integrated intensities of X-ray diffraction peaks using chromium Kα or molybdenum Kα X-radiation.
ASTM E1426
– Standard Test Method for Determining the X-Ray Elastic Constants for Use in the Measurement of Residual Stress Using X-Ray Diffraction Techniques
Test method for experimentally determining the x-ray elastic constants (XEC) for the evaluation of residual and applied stresses by x-ray diffraction techniques.
SAFRAN DMC0107
– Fatigue Test Specimen Machining Reference
Instructions defining the machining conditions for fatigue test specimens and the residual stress requirements to which the finished specimen must conform.
GE P1TF79
– Metallic Test Specimen Preparation, Low Stress
Specification presenting requirements for the preparation of low residual stress test specimens using machining, grinding, and polishing techniques as well as the residual stress requirements to which the finished specimen must conform.
GE S294
– Periodic Process Verification Testing Of Critical Forged Parts
Specification with procedures and guidelines for periodic testing of forged critical Life Controlled parts as well as the residual stress requirements to which the finished specimen must conform.
BS EN 15305
– Test Method For Residual Stress Analysis By X-Ray Diffraction
European Standard describing the test method for the determination of macroscopic residual or applied stresses non-destructively by X-ray diffraction analysis in the near-surface region of a polycrystalline specimen or component.
ASTM E2860
– Standard Test Method for Residual Stress Measurement by X-Ray Diffraction for Bearing Steels
Test method for experimentally determining macroscopic residual stress tensor components of quasi-isotropic bearing steel materials by X-ray diffraction (XRD).
GE P29TF25
– Acceptability Limits For Surface Integrity
Specification that includes requirements applicable to localized surface areas of finished parts, as designated on part drawing, which are subjected to material removal process as well as the residual stress requirements to which the finished specimen must conform.
Pratt & Whitney N-71
– X-Ray Residual Stress Analysis For Bearing Components Of M50 And M50NiL Alloys
Procedure providing residual stress measurement requirements of bearing components of M50 and M50NiL alloy.
ASTM G61
– Standard Test Method for Conducting Cyclic Potentiodynamic Polarization Measurements for Localized Corrosion Susceptibility of Iron-, Nickel-, or Cobalt-Based Alloys
Test method detailing cyclic potentiodynamic polarization measurements to determine relative susceptibility to localized corrosion (pitting and crevice corrosion) for iron-, nickel-, or cobalt-based alloys in a chloride environment.
ASTM G44
– Standard Practice for Exposure of Metals and Alloys by Alternate Immersion in Neutral 3.5 % Sodium Chloride Solution
Practice for making alternate immersion stress corrosion tests in 3.5 % sodium chloride (NaCl).
ASTM G36
– Standard Practice for Evaluating Stress-Corrosion-Cracking Resistance of Metals and Alloys in a Boiling Magnesium Chloride Solution
Practice for conducting stress-corrosion cracking tests in a boiling magnesium chloride solution.
ASTM G31
– Standard Guide for Laboratory Immersion Corrosion Testing of Metals
Guide describing the factors that influence laboratory immersion corrosion tests, particularly mass loss tests.
ASTM G71
– Standard Guide for Conducting and Evaluating Galvanic Corrosion Tests in Electrolytes
Guide for conducting and evaluating galvanic corrosion tests to characterize the behavior of two dissimilar metals in electrical contact in an electrolyte under low-flow conditions.
ASTM E18
– Standard Test Methods for Rockwell Hardness of Metallic Materials
Test method for determination of the Rockwell hardness and the Rockwell superficial hardness of metallic materials by the Rockwell indentation hardness principle.
ASTM E384
– Standard Test Method for Microindentation Hardness of Materials
Test method for determination of the microindentation hardness of materials.
ASTM E92
– Standard Test Methods for Vickers Hardness and Knoop Hardness of Metallic Materials
Test method for determination of the Vickers hardness and Knoop hardness of metallic materials by the Vickers and Knoop indentation hardness principles.
ASTM E2789
– Standard Guide for Fretting Fatigue Testing
Guide of general requirements for conducting fretting fatigue tests and reporting the results
ASTM D3720
– Standard Test Method for Ratio of Anatase to Rutile in Titanium Dioxide Pigments by X-Ray Diffraction
Test method for determination of the ratio of anatase to rutile in titanium dioxide pigments. The method is also applicable to pigment mixtures and pigmented coatings containing titanium dioxide.
ASTM D4926
– Standard Test Method for Gamma Alumina Content in Catalysts and Catalyst Carriers Containing Silica and Alumina by X-ray Powder Diffraction
Test method for determination of gamma alumina and related transition aluminas in catalysts and catalyst carriers containing silica and alumina by X-ray powder diffraction, using the diffracted intensity of the peak occurring at about 67 °2θ when copper Kα radiation is employed.
ASTM D5187
– Standard Test Method for Determination of Crystallite Size (Lc) of Calcined Petroleum Coke by X-Ray Diffraction
Test method for the determination of the mean crystallite thickness of a representative, pulverized sample of calcined petroleum coke by interpretation of an X-ray diffraction pattern produced through conventional X-ray scanning techniques.
Technician Training, Instrumentation Validation and Test Sample Tracking
Lambda’s technicians are required to undergo extensive training. Technicians must pass both written and procedural tests for each procedure per ISO 17025.
Lambda has a stringent validation schedule for all of its instrumentation. An assortment of proficiency standards, specific to each instrument, is used for validation of the measurement equipment and verification of technician proficiency.
Lambda has specific procedures written for the tracking of test samples from the moment the sample is received to when it is shipped following testing. Furthermore, Lambda understands that the proprietary nature of the customer’s component design is very important. We treat every test sample as proprietary to the customer. Lambda has several proprietary information or non-disclosure agreements on file.