Controlled Impact Burnishing
Controlled Impact Burnishing (CIB™) is a patented Lambda Technologies Group process for applications with rough surfaces, difficult to machine pieces, and hard to reach areas.
In addition to mitigating many different types of damage mechanisms through the application of engineered residual compression, Controlled Impact Burnishing:
- Easily adapts to welds and castings or surfaces with other irregularities
- Allows complete control of coverage density
- Requires no surface coatings
- Produces no debris during treatment
CIB treats the vulnerable areas of the component with highly controlled impacts to impart a deep, stable layer of beneficial compressive residual stress. The depth, magnitude, and distribution of the compression are explicitly designed for the requirements of each component and application.
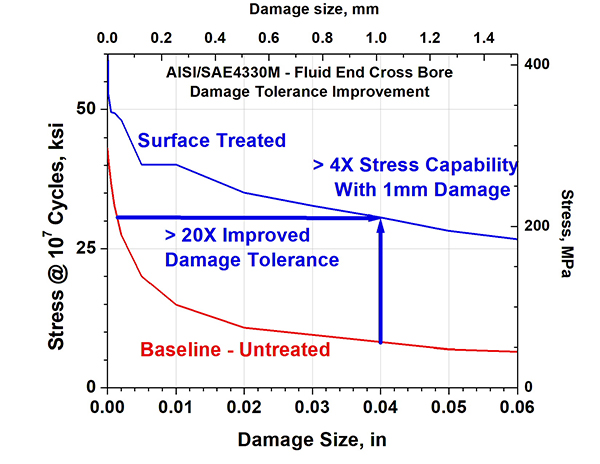
Fluid Ends Damage Tolerance Improvement by 20x
How is CIB different from other surface treatments?
- Quality Control better than Six Sigma: CIB is 100% closed loop monitored with component tracking, automatic, immediate acceptance testing, and statistical process control
- Accurate & Repeatable: Robotically controlled, ensuring a uniform, repeatable production process
- Turn-Key Production: Easily performed on the shop-room floor, requiring no remote facilities, minimal operator intervention, and allowing fewer chances for human error
- Single Cycle Processing: CIB requires only one processing cycle regardless of the depth of compression required
Applications for CIB Include:
- Impeding stress corrosion crack propagation in welded structures
- Improving metal fatigue resistance in critical fusion zones
- Mitigating fretting fatigue cracks at the conjunction of components with irregular geometries
Read more about our CIB applications in our case studies or contact us to learn how CIB can improve the performance of your component.