Case Studies
Lambda has used engineered compression and process optimization to improve component performance in applications all over the world. These are just a few of our success stories. Contact us to improve the performance of your component.

Gas Turbine Vane
Low Plasticity Burnishing (LPB®) improves foreign object damage (FOD) tolerance and high cycle fatigue endurance limits while completely mitigating cracking along the trailing edge of the Ti-6Al-4V Alloy F402 First Stage Low-Pressure Compressor (LPC1) Vane used in the Harrier jet.
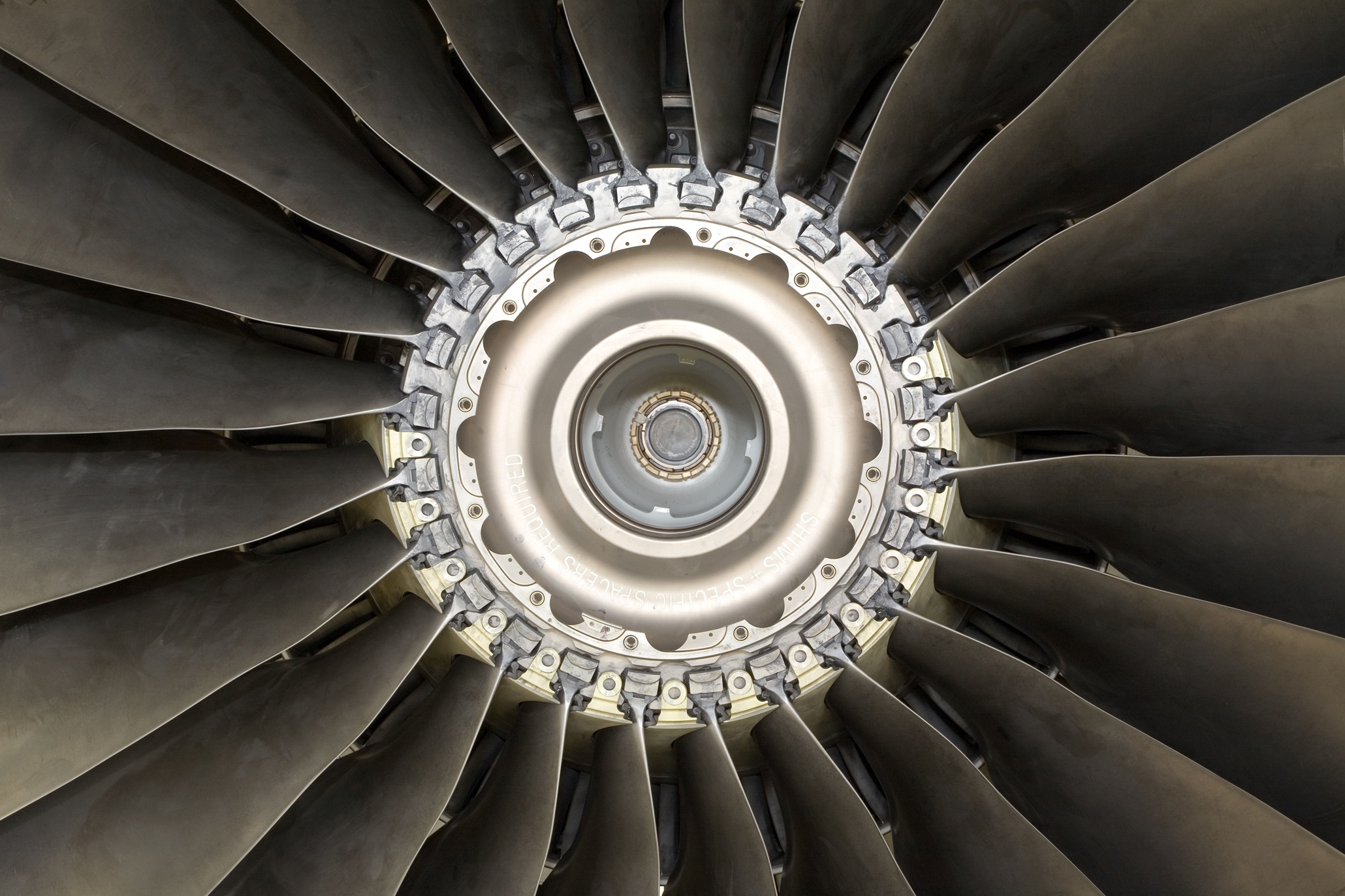
Gas Turbine Blade
Using low plasticity burnishing (LPB®), Lambda engineers apply a deep, stable layer of designed residual compression to the dovetail region of CFM56-7 HPC1 turbine blades. By putting the edge of contact region in compression much deeper than the shallow shear cracks formed by fretting, fatigue cracks cannot propagate and the chance of failure is eliminated.
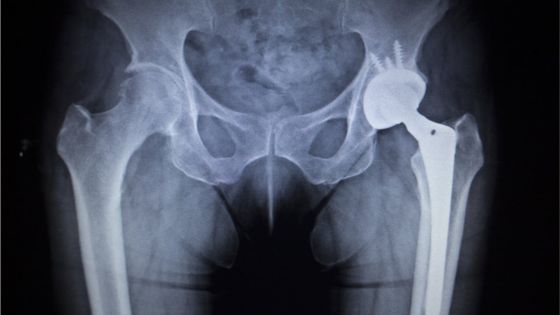
Biomedical Implants
Over seven million US citizens have regained their mobility because of hip or knee implant technology. The popular modular titanium prosthesis systems can be vulnerable to fretting fatigue in the edge-of-contact region of the tapered joint, leaving the implant vulnerable to fatigue fracture and, potentially, failure. LPB® treatment of high-stress areas in these implants increases the fatigue life and eliminates the occurrence of failure from fretting-induced fracture.
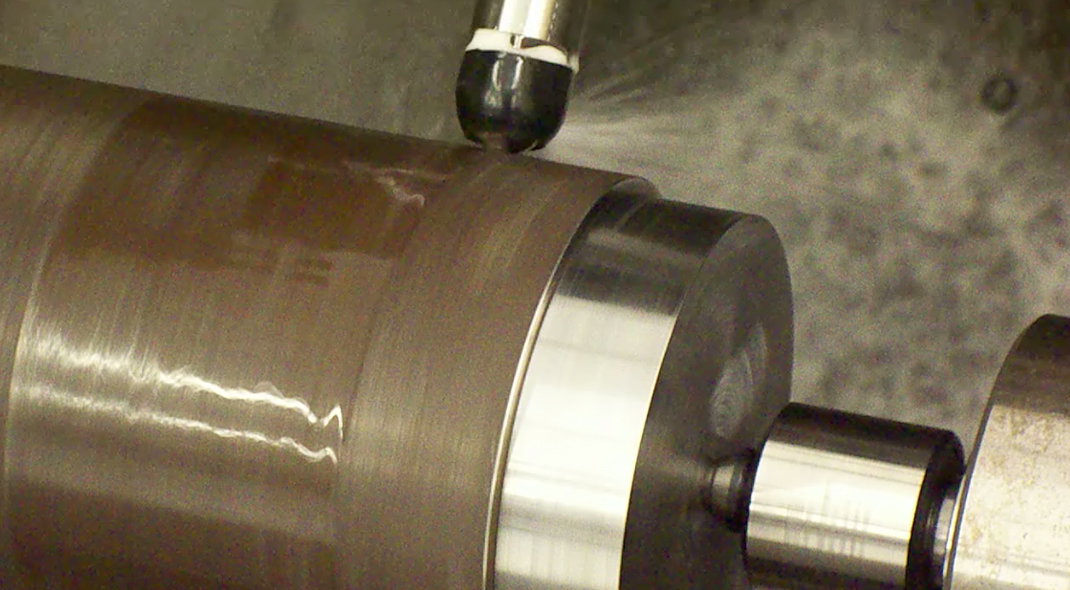
Downhole Couplings
By introducing a deep, stable layer of compressive residual stress, Lambda’s low plasticity burnishing (LPB®) technology has been shown to eliminate SSC and SCC in high strength steels. LPB offers unprecedented control of residual stresses, providing superior protection for a fraction of the cost of SCC resistant alloys.
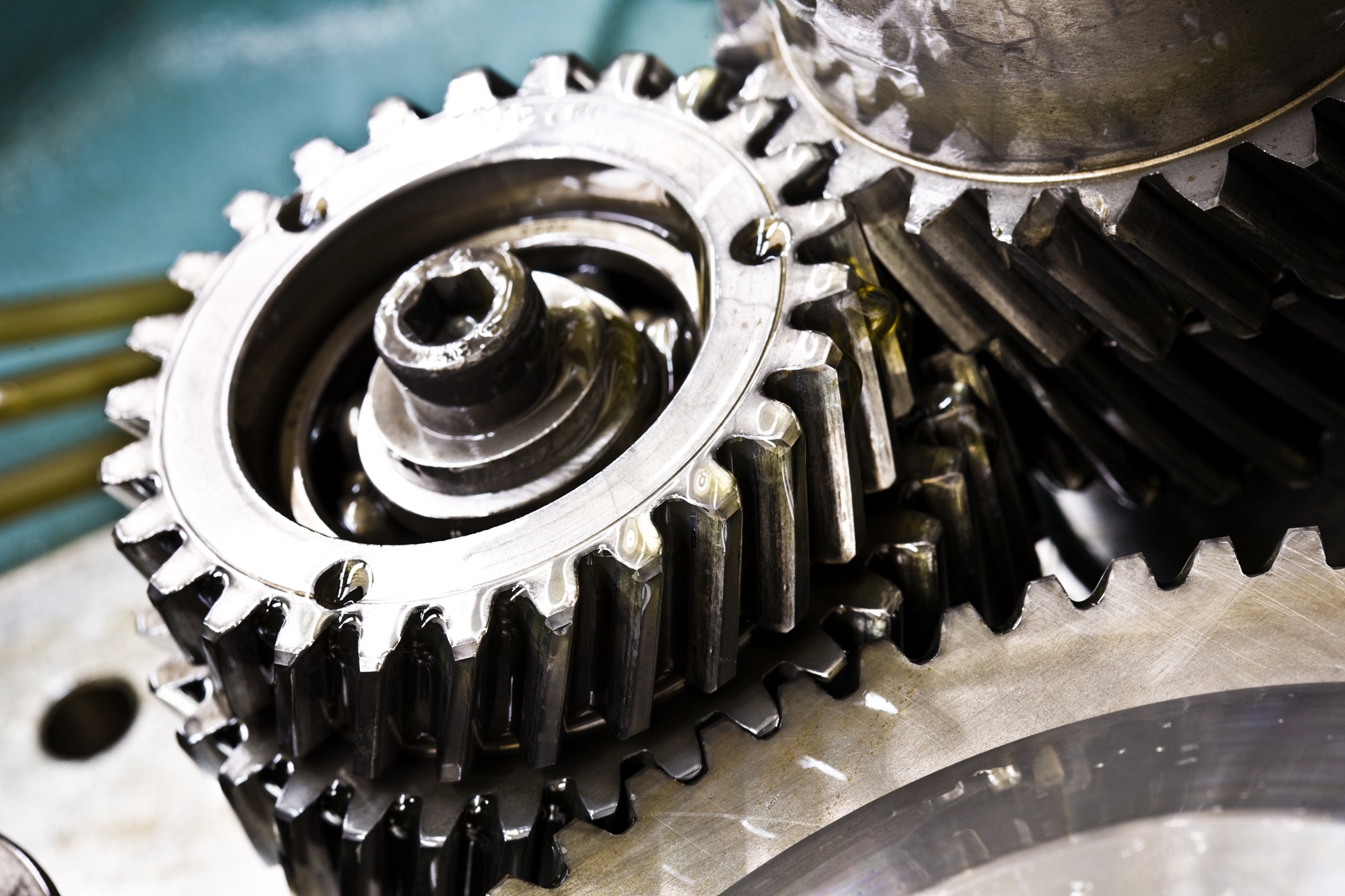
Carburization of Gear Steels
Carburization is frequently used to harden the metal surface of gears and shafts by increasing carbon content. Carburization time can be lengthened to increase case depth, but this can increase retained austenite, which is unstable at room temperature and reduces contact fatigue strength. The fatigue properties of carburized components can be significantly improved by optimizing the carburization process and the resulting compressive residual stress profile.
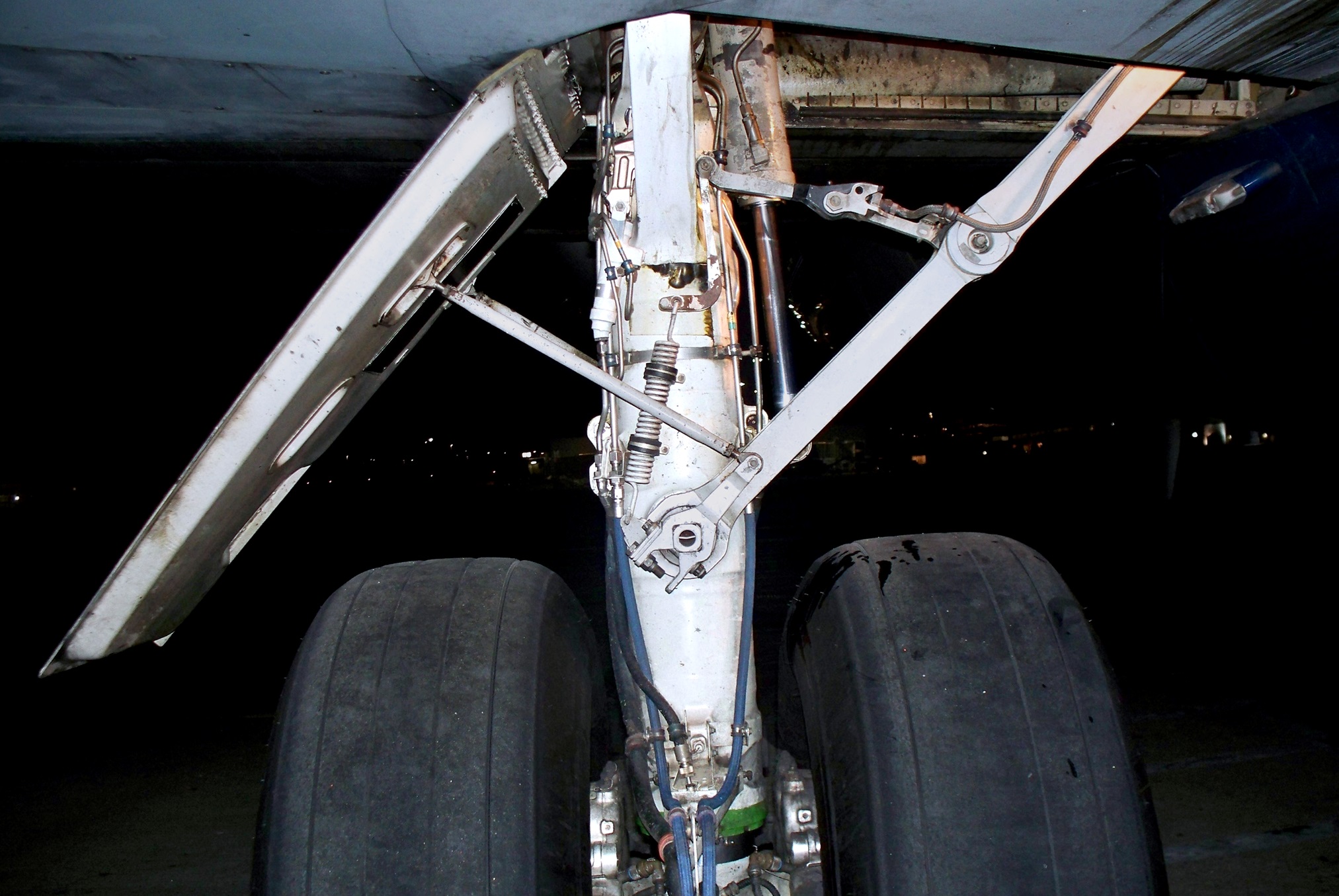
Main Landing Gear
High-strength steel is used in landing gear because of its unique combination of extreme strength and fracture resistance. Regular impact and braking during landing causes vibratory stresses in the cylinders of some types of landing gear, referred to as “gear walk,” and can potentially lead to fatigue failure. LPB® was applied to MD-88 landing gear in situ in the hangar during regularly scheduled maintenance. The process significantly improved the fatigue strength and saved more than $10 million on inspections alone.
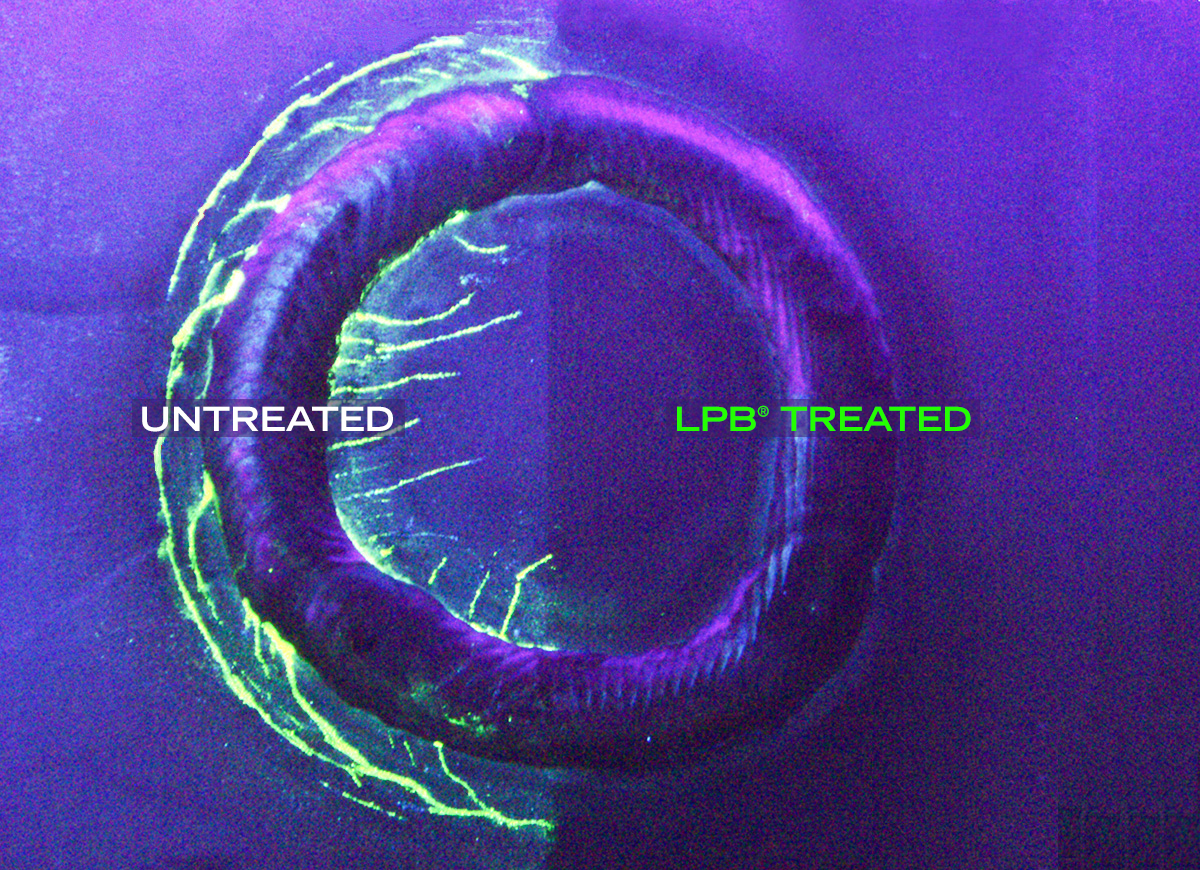
Nuclear Welds
Lambda developed a solution to completely eliminate stress corrosion cracking in the closure welds, ensuring nuclear waste containers could last for the entire designed component life. Using Controlled Plasticity Burnishing (CPB™), a deep, stable layer of engineered residual compression was applied to the closure welds, eliminating the tension in the HAZ. This prevents shallow cracks from propagating and effectively eliminates stress corrosion cracking.
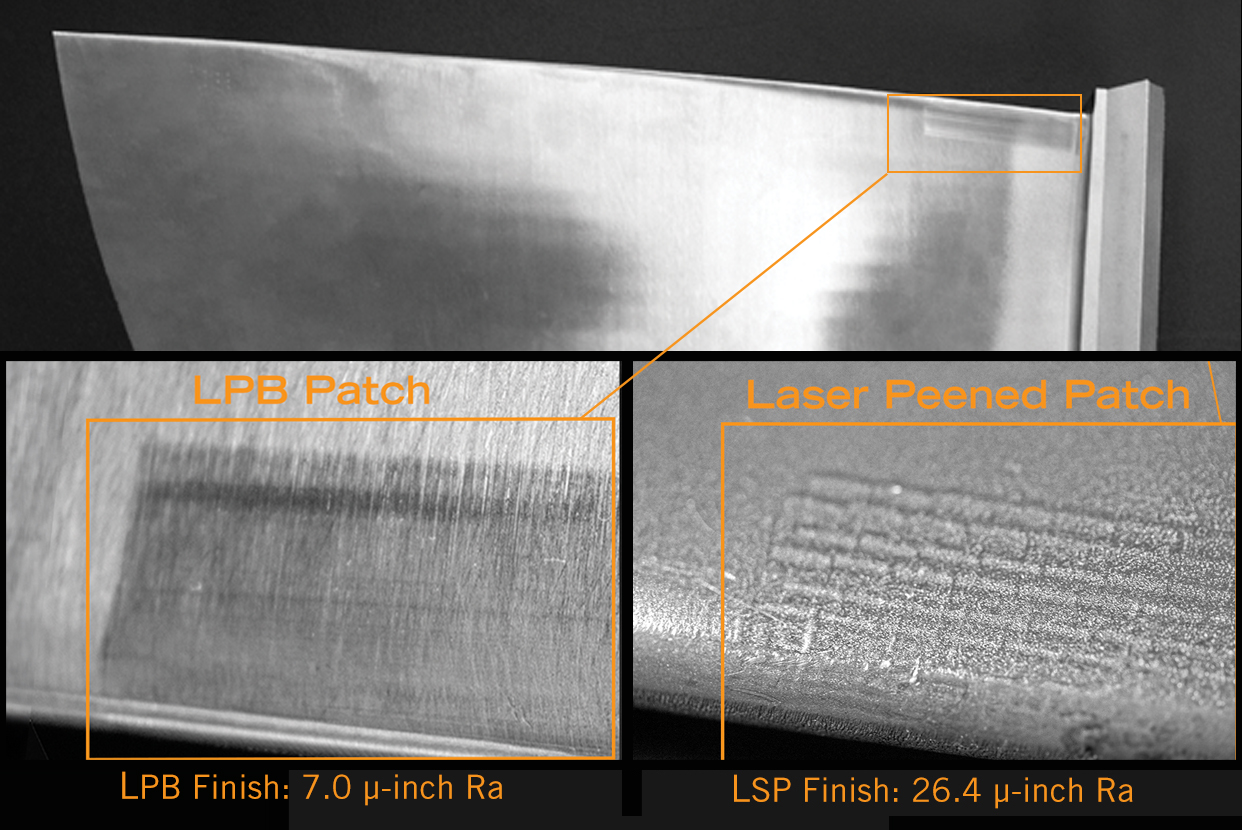
LPB vs LSP: Ground-Based Gas Turbine Blade
Lambda Technologies developed a solution to extend the fatigue life and improve the damage tolerance of the R0 blades. Using low plasticity burnishing (LPB®), Lambda Technologies’ engineers applied a deep, stable layer of engineered compression to the leading edge region of the blades. The goal of this project was to match or exceed the compression of laser peened blades and improve damage tolerance.
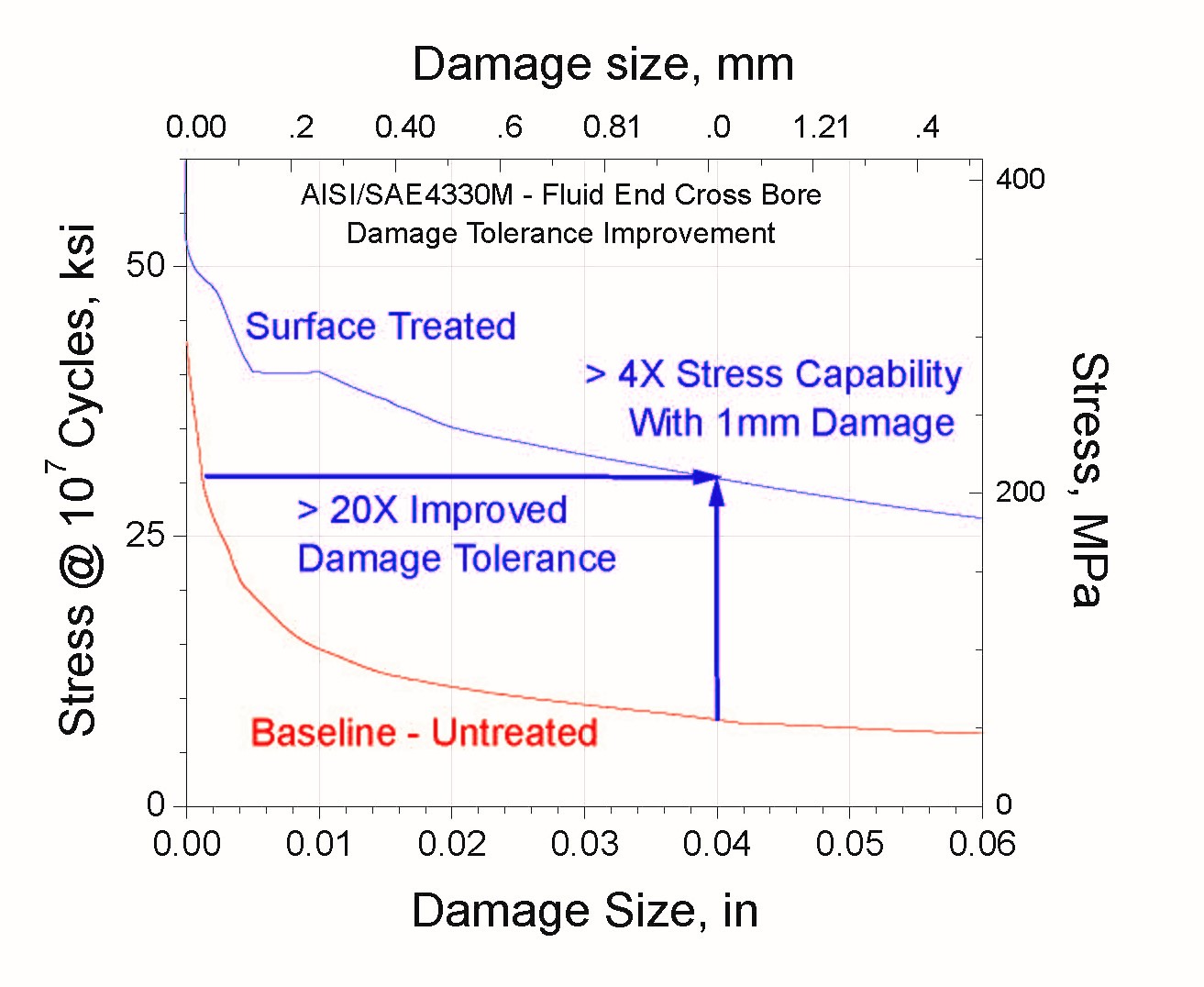
Hydraulic Fracturing Pump Fluid Ends
Controlled Impact Burnishing (CIB™) is a patented Lambda process for applications with rough surfaces, difficult-to-machine pieces, and hard-to-reach areas. Applying this surface treatment to the cross-bore regions of hydraulic fracturing pump fluid ends gives a deep, stable layer of engineered residual compression deeper than the shallow cracks initiated by stress corrosion or fatigue. A huge increase in damage tolerance was achieved in both AISI 4340 steel and 17-4PH stainless steel fluid ends.
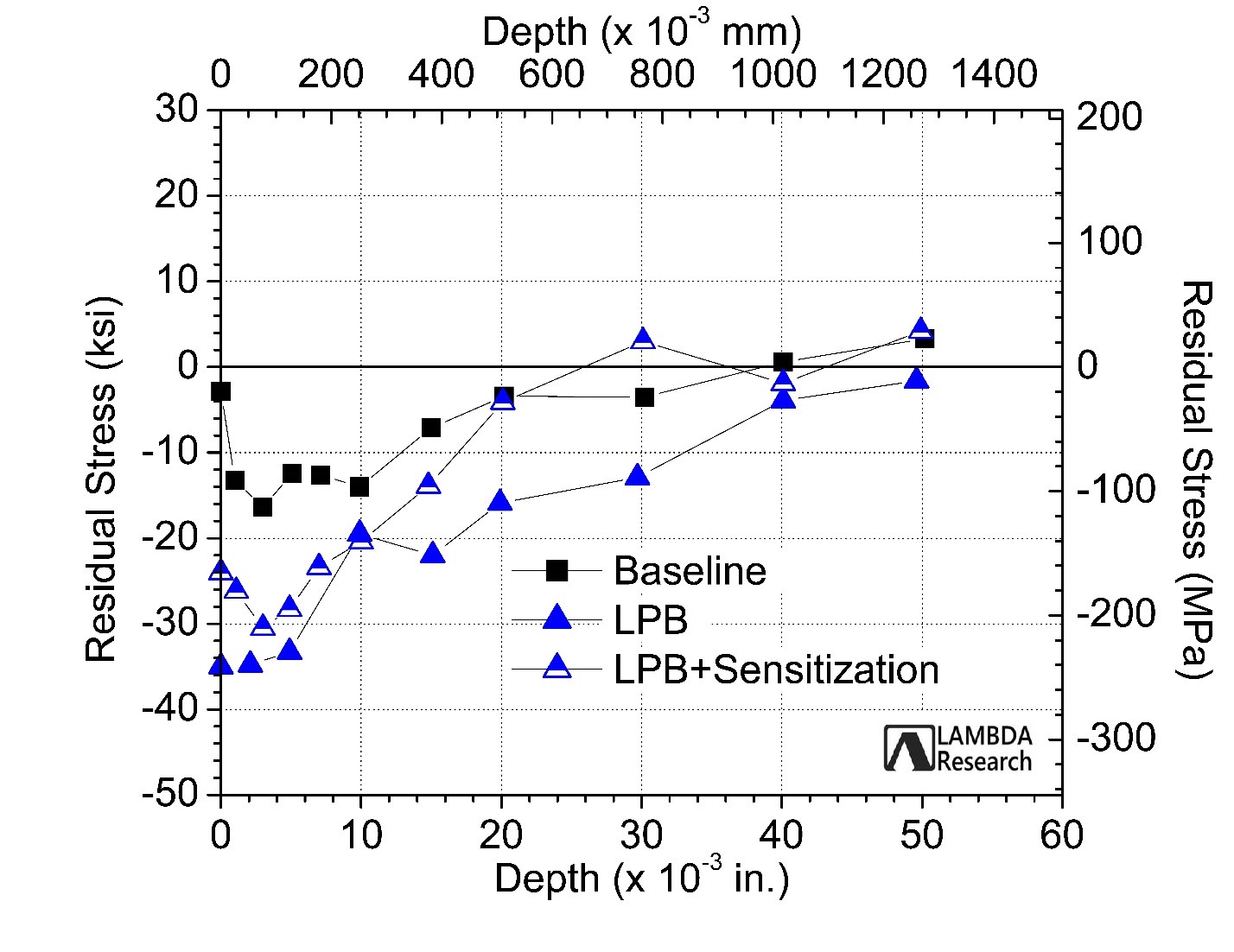
Sensitized Marine Aluminum
AA5083-H116 is a commonly used alloy in ship applications. Alloys of this series are prone to low-temperature sensitization, which leads to beta-phase (Mg2Al3) precipitation along grain boundaries. This increases susceptibility to stress corrosion cracking (SCC) and corrosion fatigue (CF), particularly around the Heat Affected Zones of welds. Low plasticity burnishing (LPB®) was applied to samples and then subjected to residual stress and corrosion testing. Results showed improved corrosion fatigue performance for the LPB processed samples, with an endurance limit increase of about 70% over baseline.
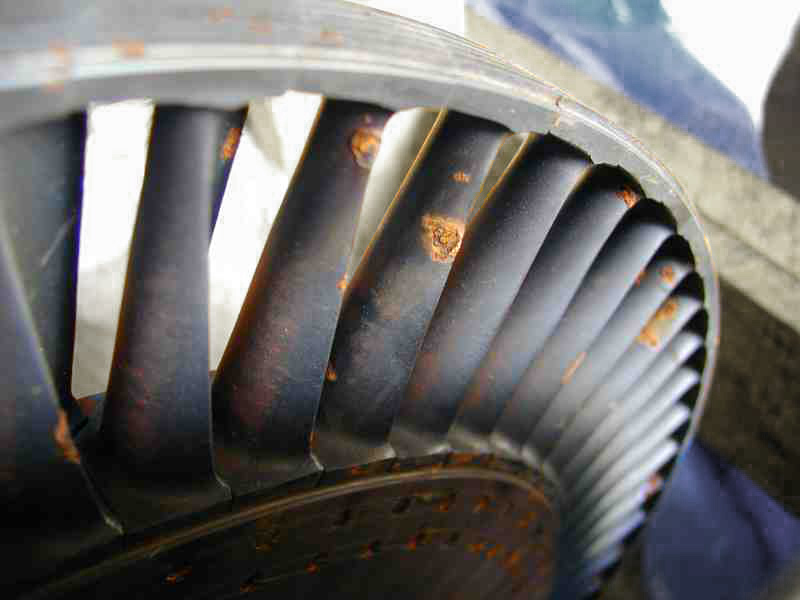
Steam Turbines
Steam turbines provide a huge percentage of the world’s electricity, making them the backbone of power generation. Repeated exposure to high vibratory stresses and extreme steam environments leads to stress corrosion cracking (SCC) and fatigue failure in the turbine blades. Applying a deep, stable layer of engineered compression with Low Plasticity Burnishing (LPB®) in high stress areas of turbine blades significantly extends component life and reduces operating costs.
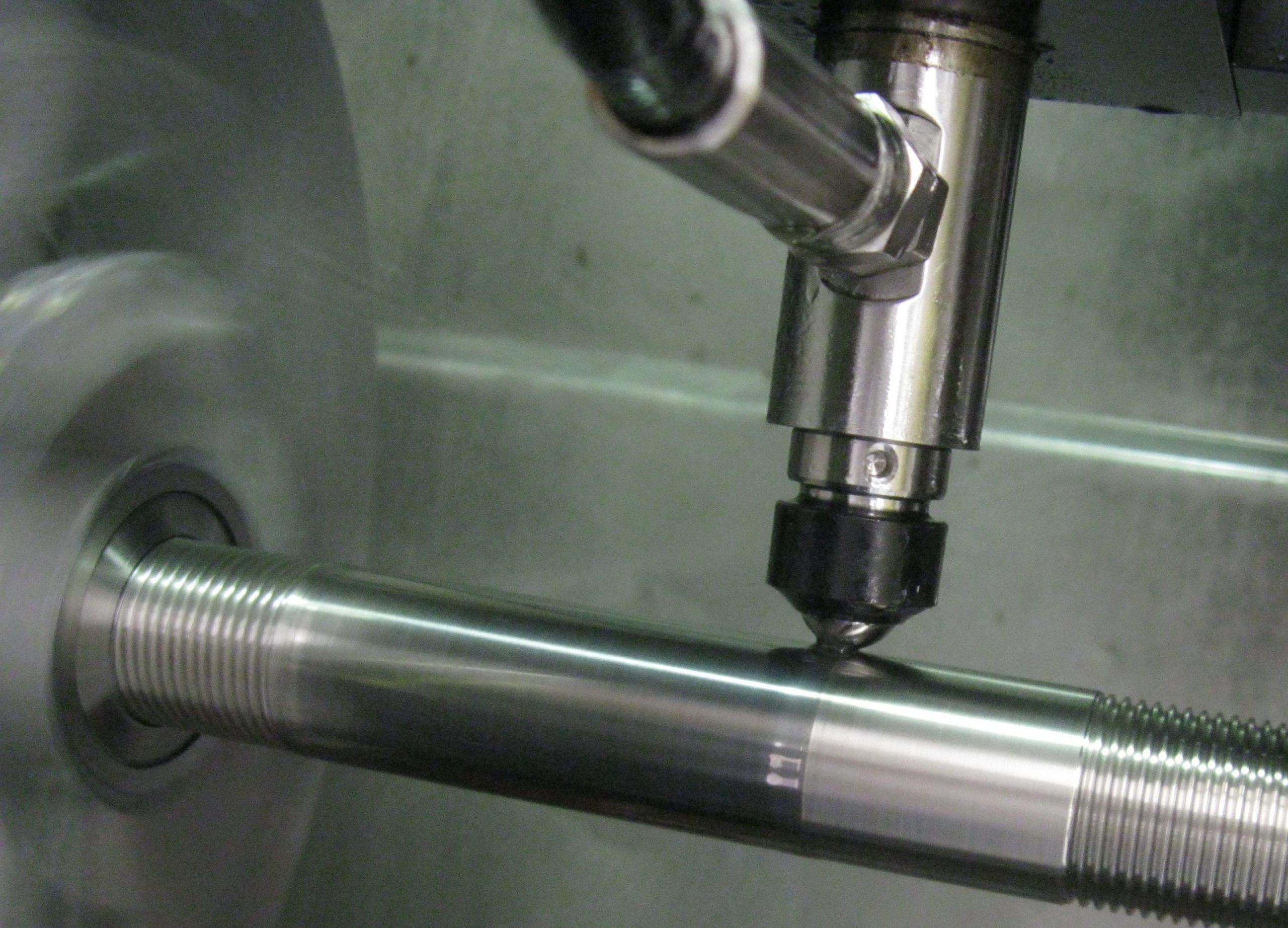
Turbine Bolts
Tie rod bolts that connect the stages of ground-based turbines can be susceptible to fretting fatigue at the edge of contact between the rotors and tie rod landings. This can potentially lead to failure of the bolts within just the first few years in service. With low plasticity burnishing (LPB®), bolts can remain in service for the entire design life of the turbines. In this application, the manufacturer has saved over $40 million so far since introducing LPB to their production process.
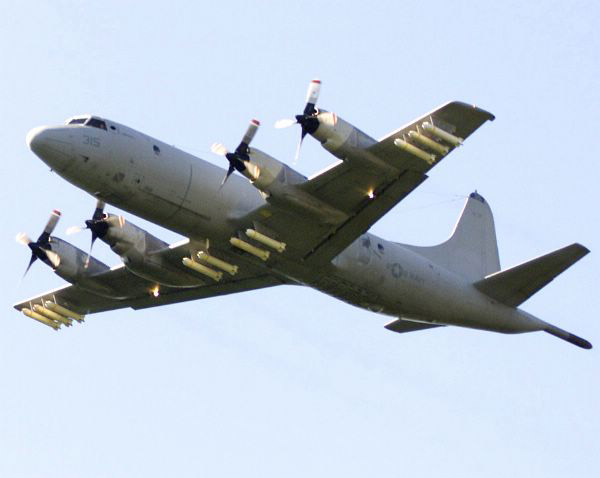
Structural Aircraft Components
The P-3 Orion aircraft are currently averaging approximately 24,000 flight hours, 16,500 hours past the designed service life. Full-scale pressurization testing showed that several forged floor beams are prone to fatigue damage due to stress concentrations from machined cutouts. Replacement of the components is impossible, so a program was implemented to increase fatigue life and eliminate stress-related fractures with LPB®.
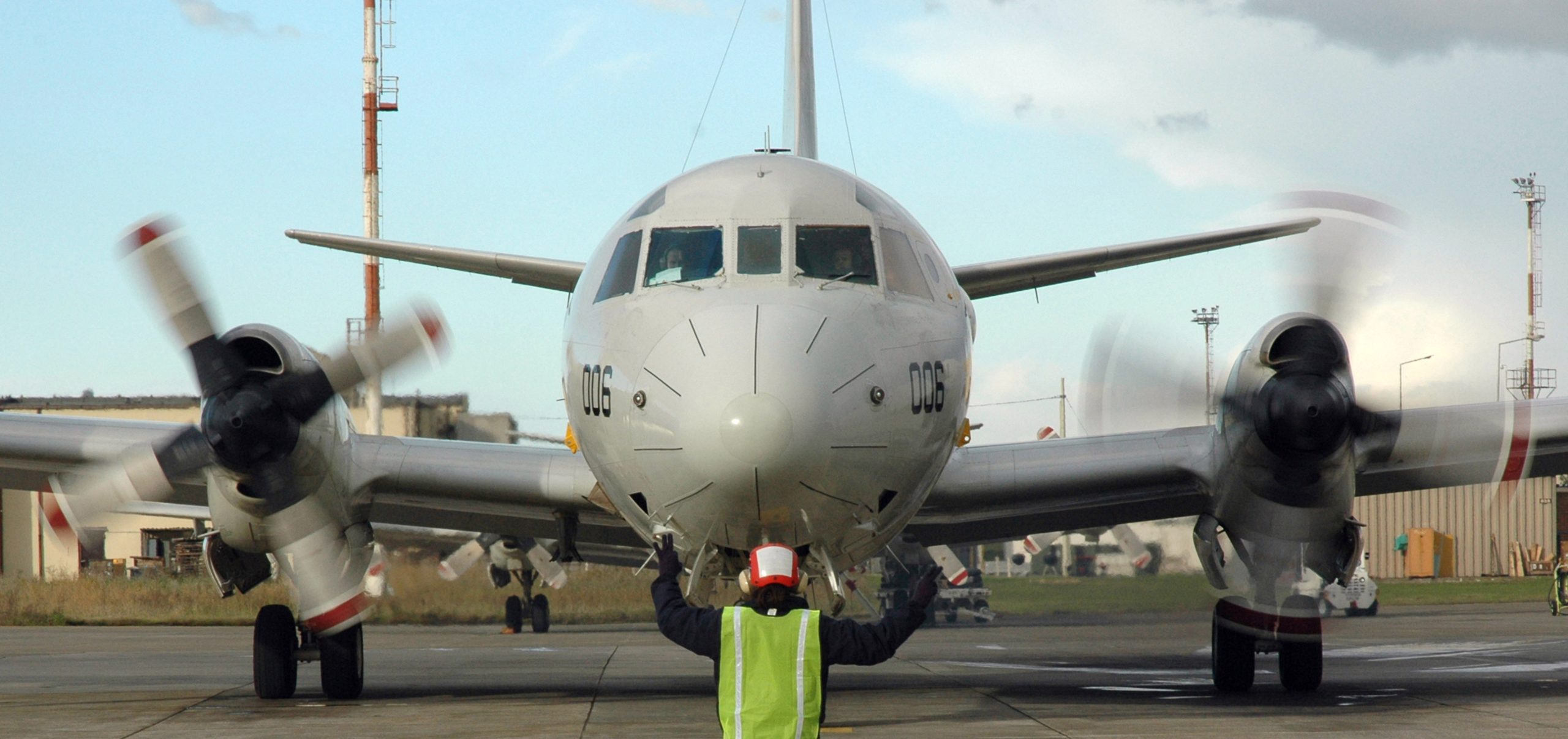
Propeller Taper Bore
Low Plasticity Burnishing (LPB®) mitigates stress corrosion cracking (SCC) and improves corrosion fatigue strength while increasing the service life and reducing the total maintenance costs of the aluminum alloy 7076-T6 propeller for the U.S. Navy’s maritime patrol aircraft.
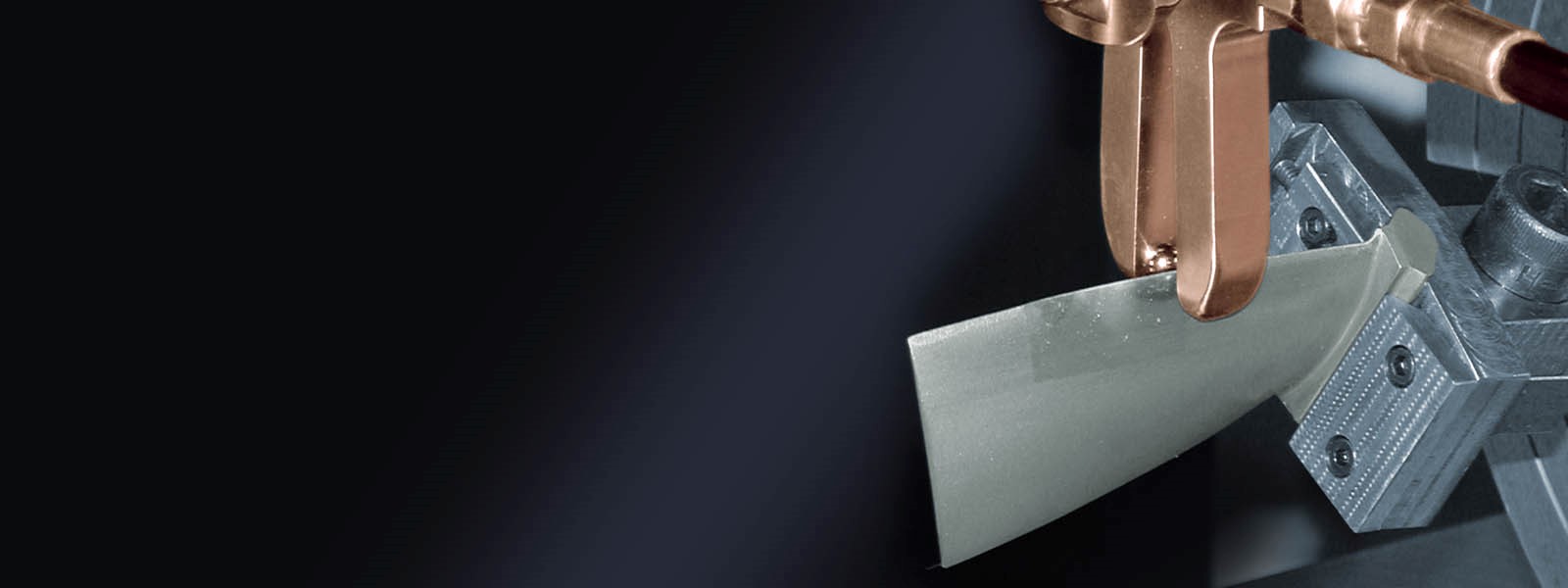
Turboprop Compressor Blade
Low Plasticity Burnishing (LPB®) mitigates pitting, diminishes foreign object damage (FOD), and improves damage tolerance and high cycle fatigue (HCF) while reducing the replacement costs of the 17-4 PH Stainless Steel 1st Stage Compressor Blade in the T56 Turboprop Engine.
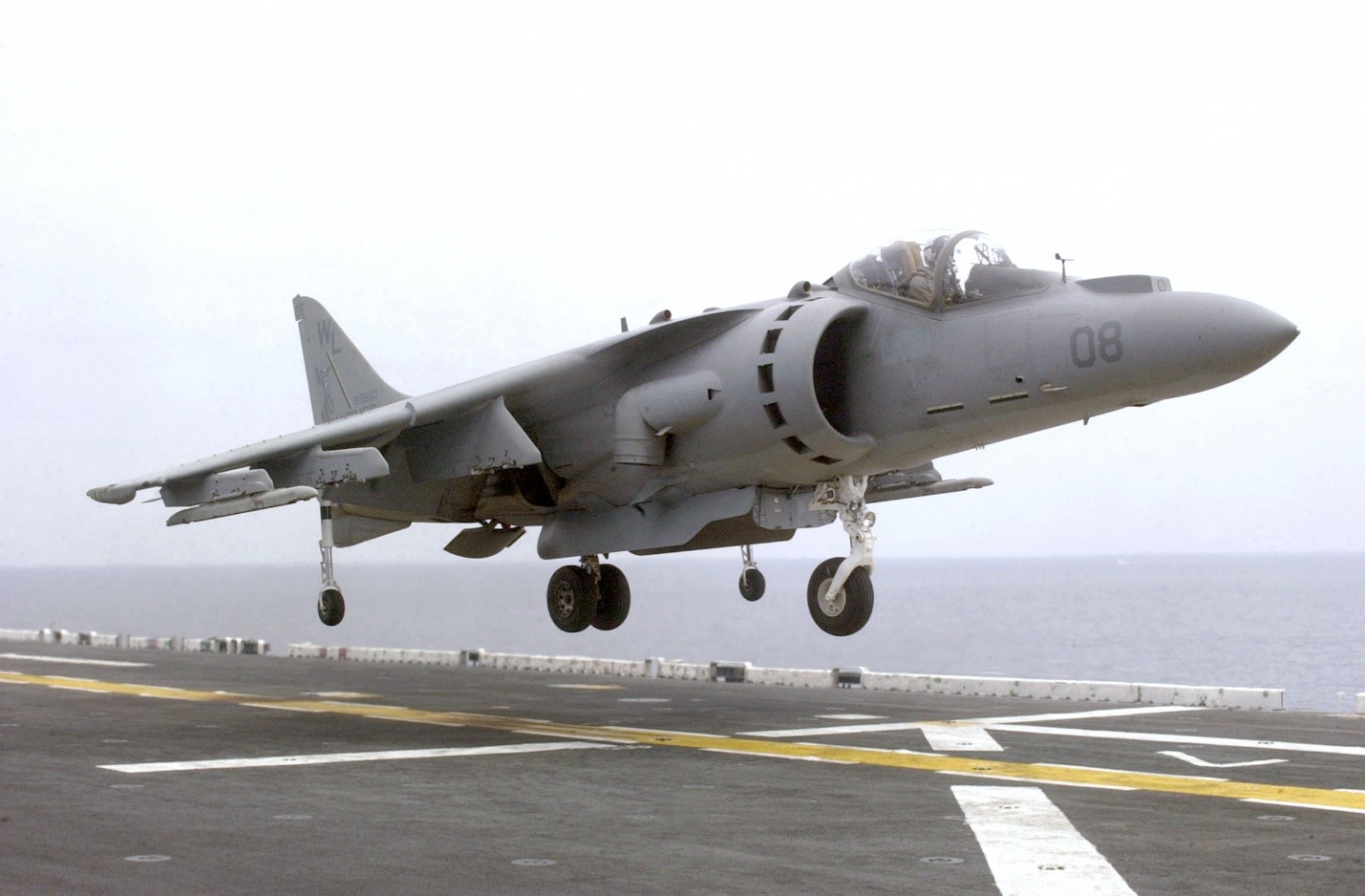
Jet Engine Blade
Low Plasticity Burnishing (LPB®) enhances foreign object damage (FOD) tolerance and improves fatigue performance of the leading and trailing edges of the LPC Stage 1 Blade in the F402-RR-408 engine used in the Harrier.