SHOT PEENING
Shot peening is the oldest, most widely used surface treatment method to impart shallow compression into the surface of components. It is done to help mitigate failure mechanisms, such as metal fatigue, stress corrosion cracking, pitting, fretting, and foreign object damage, among others.
Metallic or ceramic shot impacts the surface of a component, producing indentations. Subsurface compression combined with lateral displacement of surface material around each dimple creates a low magnitude layer of compressive residual stress.
Common Issues with Shot Peening
Whether air blast, wheel or ultrasonic, shot peening relies upon random impacts of shots. Treated regions of the part will receive numerous impacts before impacts to adjacent areas occur at all. The result is a non-uniform and highly cold-worked surface.
- Cold working can exhaust the ductility of work hardened material, leaving a brittle surface layer.
- Damage in the form of “laps and folds” creates stress concentrations that reduce fatigue performance.
- Components exposed to elevated temperatures or mechanical overload will relax more completely and much faster if they are highly cold-worked versus a low cold-worked surface at the same state of compressive stress.
Shot Peening Optimization is an option to offset some of the common issues with shot peening. With shot peening optimization, peening specifications are tailored for components to achieve optimum fatigue results and faster processing times.
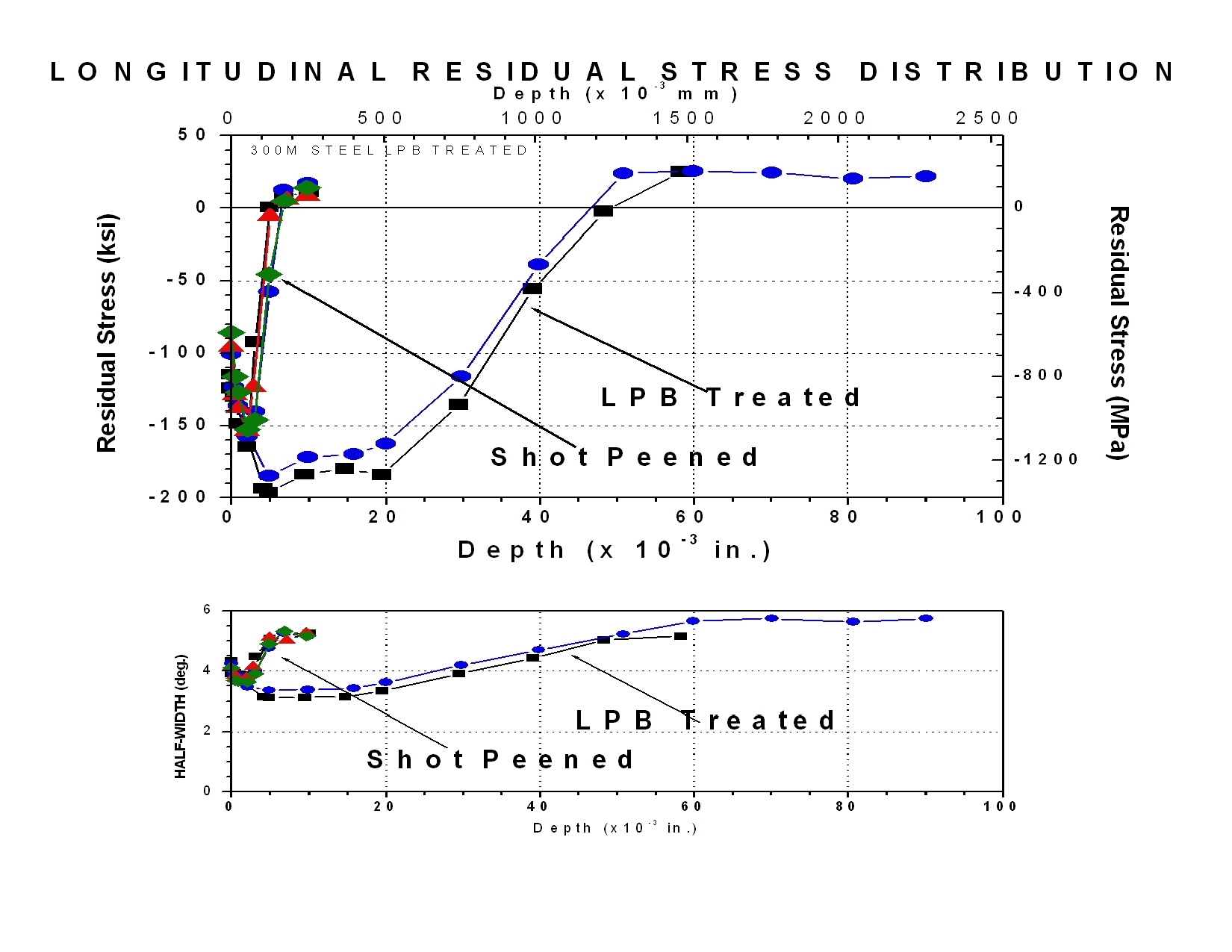
Shot Peening vs LPB Shot Peening
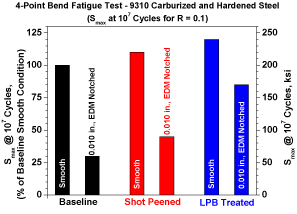
Thermal Stability
Alternate Services Offered by Lambda Technologies Group
Low Plasticity Burnishing (LPB®) >
introduces beneficial compressive residual stress into materials with minimal cold work. This allows the compression to better withstand high temperatures, repetitive loading and corrosive conditions.
Controlled Plasticity Burnishing (CPB™) >
is a variation on our award-winning LPB treatment, specifically designed for applications where low cold work isn’t necessary.
Controlled Impact Burnishing (CIB™) >
is a process to treat vulnerable areas of a component with highly controlled impacts to impart a deep, stable layer of beneficial compressive residual stress.