Failure Analysis
Component failures are costly, by determining the cause using Failure Analysis, your company can save millions in lost revenue and staff-hours. Lambda uses state-of-the-art equipment and advanced modeling techniques toat provide comprehensive failure analysis. Our engineers can establish the failure mechanism, calculate the stresses at failure, and provide a complete history of crack growth in your component.
How does it work?
Lambda engineers work with the client to understand the component operating conditions and all the details relating to component failure. After gathering all of the information related to a specific component failure, we apply our extensive experience using in-house testing resources to determine the cause of the failure. After determining the cause of the failure, our engineers can provide solutions to improve component strength and life.
Features:
Quantitative Fractographic Analysis
Historically, fractography has been used as a post-mortem analysis of failed components and structures. In most cases of fatigue cracking, stress corrosion cracking, and overload failure, conclusions as to the nature of the failure are based on qualitative analysis of failed parts, and recommendations are made to rectify the problem.
In some instances, a more detailed quantitative fractographic analysis may be in order. We perform a Quantitative analysis of the failure with the assistance of linear elastic fracture mechanics (LEFM), knowledge of the fatigue crack growth behavior, understanding of damage processes like SCC & creep crack growth, and any other available evidence. By using quantitative fractographic analysis, a detailed chronological account of a component’s service history with loads and cycles can be extracted.
Assessment of Stress by Examining Fatigue Striations
High Cycle Fatigue (HCF) is one of the most common failure modes of critical components. The cause of component failure must be quickly and accurately assessed in order to determine a solution. The actual stress at the failure site is often unknown since components are designed to operate well below the fatigue limit. By performing a detailed examination of the fatigue striations and applying fracture mechanics theory, Lambda provides the expertise and tools to accurately assess the stresses at the failure location.
Lambda utilizes SEM imaging of the fracture face and advanced analysis software to determine the stresses that cause fatigue failures. Lambda can conduct the analysis on a replica of the fracture face eliminating the need to have access to sensitive hardware. Using this novel technique, Lambda can quickly provide information our customers require to solve their critical issues.
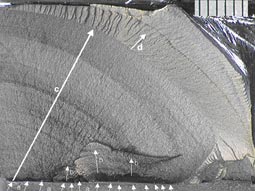
Fractography of failed component showing multiple crack nucleation sites from fretting-induced microcracks; growth of semi-elliptical cracks from surface; dominant fatigue crack growth of the corner crack; and overload fracture.
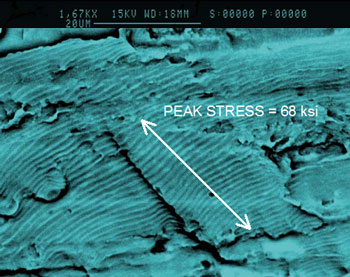
SEM image of fatigue striations of failed component.
Questions about Failure Analysis needs?